7 min reading time
What are Maintenance Types?
18 ต.ค. 2022, 10:18:18
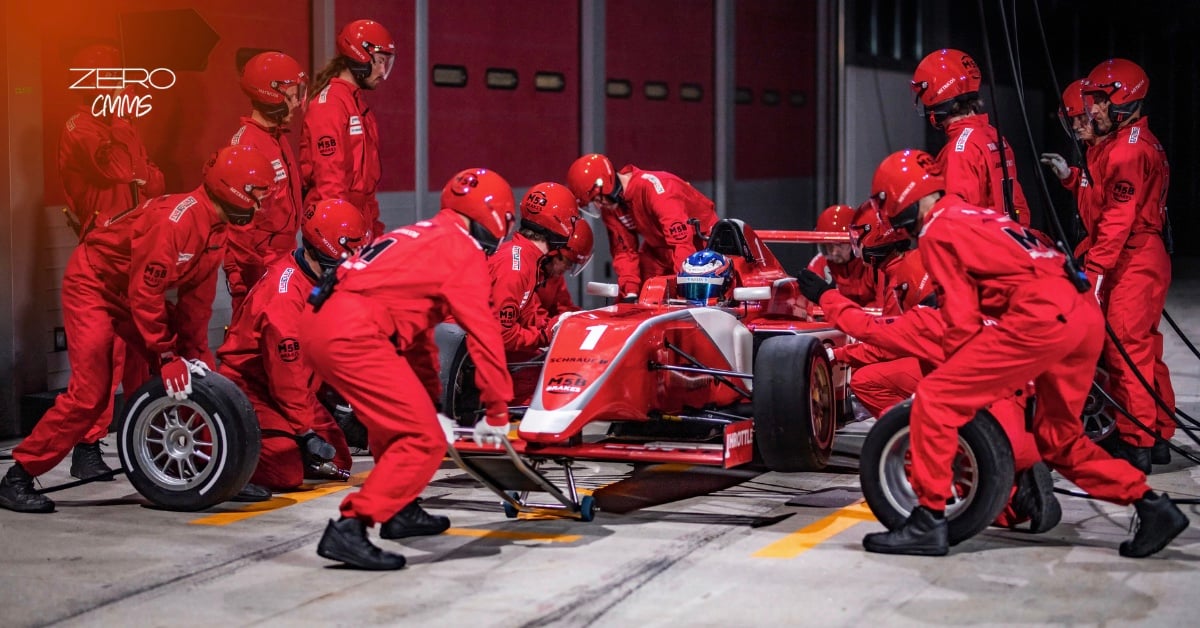
Some businesses are still running their fixed operating assets to failure and their maintenance is based solely on corrective maintenance strategy. Many business owners understand the benefits of preventive maintenance strategy; however, they often don't even consider any other types of maintenance than predetermined time-based maintenance.
Maintenance types are different versions of corrective and preventive maintenance strategies that are selected for the maintenance of fixed operating assets to achieve the strategic goals of operations and maintenance.
This blog post will explain what are the six maintenance types to consider:
- Deferred corrective maintenance
- Immediate corrective maintenance
- Predetermined time-based or meter-based maintenance
- Condition-based maintenance
- Predictive maintenance
- Prescriptive maintenance
MAINTENANCE TYPES
What Are Maintenance Types?
Maintenance types are classified by the European standard (EN 13306:2017) in two main categories:
- corrective maintenance that takes place after equipment fault has been identified and
- preventive maintenance that takes place before machine failures.
CORRECTIVE MAINTENANCE STRATEGY
Corrective maintenance strategy is also called as a run to failure strategy where maintenance is undertaken only after machines have broken down or equipment have failed in operation.
The purpose of the corrective maintenance strategy is to restore the function or condition of the fixed operating assets.
Corrective maintenance strategy is selected for fixed operating assets, whose failure is acceptable i.e. there are no significant consequences of failure to people, property, plant, or equipment, nor the environment. And there are no technically or economically feasible ways to prevent equipment failures or machine breakdowns.
Corrective maintenance is classified into two categories based on their urgency:
Deferred corrective maintenance is not urgent and the execution of the maintenance tasks is delayed in accordance with given rules. Service requests created by operators or other stakeholders often trigger the creation of non-recurring deferred maintenance work orders. If the deferred corrective maintenance tasks are executed without scheduling at the same time as other maintenance tasks to save time and cost, they can be classified as opportunistic corrective maintenance. And if the deferred corrective maintenance work orders get scheduled, then they can be classified as scheduled corrective maintenance.
Immediate corrective maintenance is also called as emergency maintenance and it is carried out without delay after a fault has been detected to avoid unacceptable consequences. Failure notifications or incident reports typically trigger immediate action to reduce the asset maintenance downtime or additional damage to property, people, and environment to minimum. Maintenance planner must quickly create a non-recurring maintenance work order and allocate appropriate resources for the fast execution of the maintenance tasks.
Emergency maintenance must be avoided as much as possible and you should ensure that no more than 1 - 2 % of your total maintenance is emergency maintenance.
How much time, money, and energy do you spend on emergency maintenance?
PREVENTIVE MAINTENANCE STRATEGY
Preventive maintenance strategy is undertaken before machines will brake down or equipment fail in operation.
The purpose of the preventive maintenance strategy is to keep the property, plant, and equipment in good working order and operations up and running.
Preventive maintenance can be classified into four categories:
Predetermined maintenance is carried out in accordance with established intervals of time or number of units of use. Preventive maintenance work orders are often defined by manufacturers, who require regular time-based or meter-based service intervals to keep warranty effective until the expiry date. Predetermined maintenance strategy doesn't take the condition of the fixed operating assets into consideration, which may result in unnecessary maintenance and increased maintenance costs.
Condition-based maintenance include assessment of physical conditions, analysis and the possible ensuing maintenance actions. Condition-based maintenance tasks can be triggered based on operator observation, inspection, measurement or testing and condition-data collected automatically from data sources.
The purpose of condition-based maintenance strategy is to look for physical evidence that a machine breakdown or equipment failure is occurring or will occur in the near future.
Photo by Jorge Ramirez on Unsplash
The purpose of the predictive maintenance is to predict when the machine will fail and then define the appropriate preventive maintenance measures.
Prescriptive maintenance uses condition-data to build prescriptive algorithms and propose solutions with the help of machine learning and artificial intelligence. It is perhaps the most advanced approach of condition-based maintenance because is proposes appropriate solutions in addition to predictions based on the condition of the machines.
What maintenance types should I use for my fixed operating assets?
Selecting corrective maintenance strategy and letting your fixed operating assets run to failure can be expensive; however, it may be the right strategy for lower-risk assets that can't affect the operational availability, reliability, or quality of your operations. Or there is no technically nor economically feasible way to prevent failures.
In order to reduce the cost of running your assets to failure you can apply the so called failure finding maintenance approach to conduct inspections aimed at detecting hidden equipment faults and machine failures which do not affect operations directly. If any equipment faults or machine failures are detected during inspections, maintenance work orders should be created to repair the machinery and equipment before they cause more damage to other property, plant, and equipment.
Predetermined time-based or usage-based maintenance strategy must be applied to fixed operating assets according the requirements and instructions of manufacturers and suppliers, while the warranty period is still valid.
A warranty period is the period of time that warrant free repair and adjustment services in case of a malfunction occurred under normal use that has followed instruction manuals.
After the warranty has expired it's up to you to continue with the manufacturer's recommended predetermined maintenance strategy or change to another one.
Risk-based maintenance is an approach to help you decide what type of maintenance strategy to choose for your fixed operating assets.
You can use risk assessment methodologies to assign your assets to those that carry the highest risk levels and those that have the lowest risk in case of a machine breakdown or equipment failure.
Based on the outcome of the risk assessment you can allocate more frequent inspections and preventive maintenance for assets that have a relatively higher risk and a very high consequence of failure. Lower-risk assets can be allocated for less frequent inspections and preventive maintenance.
After you have selected the best maintenance strategy for your fixed operating assets you should develop the preventive maintenance programs. There are 7 key components your maintenance programs should include. After you have developed your preventive maintenance programs you can optimize them to save cost.
Blog Posts
What Is Condition-based Maintenance?
Condition-Based Maintenance or CBM in short is a type of Preventive Maintenance (PM) strategy where...
What Is Preventive Maintenance?
Preventive maintenance is a maintenance strategy selected for critical operating fixed assets to...
What Is Predictive Maintenance?
Predictive Maintenance or PDM in short is a type of Preventive Maintenance (PM) strategy where the...