Photo by Ibrahim Boran on Unsplash
I recall one of my first experiences with poor maintenance management vividly. I had just landed my dream job at a coveted company, and within my first week there, their main production machine broke down. My new colleagues shared a collective sigh, as this was not an uncommon occurrence. What followed was a week-long headache of halting production, attending to frustrated clients, and scrambling to repair the machine on a limited budget.
That's when I realized, the famous saying: "An ounce of prevention is worth a pound of cure" by Benjamin Franklin, who famously advised fire-threatened Philadelphians in 1736, really did hold some truth.
Clearly, preventing fires is better than fighting them, but to what extent can we protect ourselves from machine breakdowns?
As someone who has spent years building a professional career, it still amazes me how often businesses fail to grasp the significance of planned maintenance management. As a blogger focused on maintenance management, optimization, and efficiency, I find it crucial to emphasize and share my knowledge on this subject – an essential component that should never be overlooked, especially when it comes to long-term success.
A random fact I stumbled upon recently:
Did you know that an effective planned maintenance management strategy can save companies up to 12 - 18 % in repair costs? Now, who wouldn't want that?
The significant problem with businesses overlooking the importance of planned maintenance management is the potential for machine breakdowns and unplanned maintenance downtime that could have been easily prevented. To avoid such pitfalls, it is essential to develop and maintain a detailed maintenance plan.
So, what exactly is planned maintenance management?
"It is a proactive approach to managing and maintaining the physical operating fixed assets of a business, such as property, plant, machinery, and equipment. It involves scheduling regular inspections, servicing machines, and replacing spare parts before any major issues occur, effectively minimizing downtime and maximizing productivity."
A maintenance plan should include the following:
1. Inspection and review of property, plant, and equipment;
2. Preventive maintenance schedule;
3. Identifying equipment manufacturers and spare part suppliers and establishing relationships with them;
4. Staff training and development in maintenance practices;
5. Maintenance management system for tracking, reporting, and analyzing maintenance data.
Those who have implemented a properly developed maintenance management plan will attest to the dramatic decrease in equipment breakdowns, a boost in productivity and efficiency, and a noticeable reduction in repair costs.
As somebody who experienced firsthand the consequences of neglecting maintenance management, I urge all businesses, big or small, to give this essential business factor the attention it deserves. You might find your investment to be well worth the effort in the long run.
Of course, the journey of mastering planned maintenance management is a continuous process. No plan is perfect, and there will always be room for improvement. Remember, as ancient Chinese philosopher Lao Tzu said:
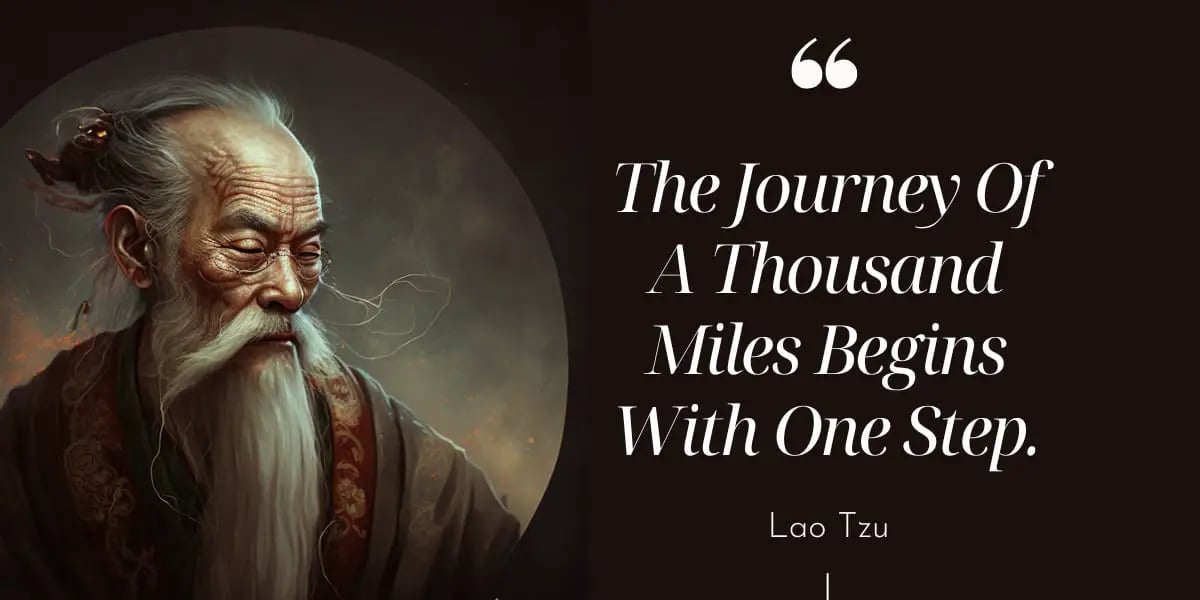
SOURCE: Lao Tzu - The Journey Of A Thousand Miles by Dynamic
So, take that step today, and witness the transformative impact of planned maintenance management on your business.