Stop Running Your Aging Assets to Failure!
Does this make you feel frustrated?
-
Operational availability is decreasing.
- Maintenance downtime is increasing.
- Sales can't reach their goals.
-
And you can't grow your business.
Markku Lyyski, CEO, Aneo Software Oy
Reduce Unplanned Maintenance Downtime to Zero!
It will take time ...
Changing your maintenance strategy and culture will take your time and energy. But you are not alone, we can help.
It's Not Easy ...
Improving the operational availability and quality of your aging assets is not easy.
-
We have seen many maintenance teams struggle to find ways to save costs and manage assets in a better way.
-
Your maintenance team deserves the tools they need to keep your assets in good working order.
-
You can get the the professional software tools that work best for you from us.
WE CAN HELP.
Our knowledge and experience is at your disposal ...-
We have helped over 10,000 users to change the way they manage and maintain their assets on a daily basis.
-
We deliver software services to hundreds of factories, plants, and mills producing goods and services 24/7.
-
Our subject matter experts have decades of experience in their fields of knowledge & expertise.
REFERENCES
"Increased competition in both core and new businesses puts pressure on margins, necessitating a focus on both cost efficiency and competitiveness in order to deliver value. Improving efficiency throughout the value chain will play a significant role. The ANEO Zero CMMS has an important role in improving the cost efficiency of our value chain and maintaining our our reliability."

"Our operations are based on competitive energy prices, competent personnel, service reliability, profitability and environmentally friendly processes. The ANEO Zero CMMS plays an important role in the maintenance of our energy production facilities and distribution networks as well as the reliability of our service operations.""
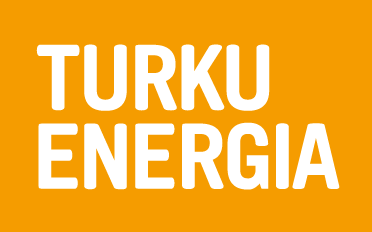
“Our goal is to reduce the time spent on developing crane inspection reports to zero and keep our crane technicians focused on delivering crane services."
.png)
“We use ANEO Zero CMMS to support our crane inspection, testing and maintenance services, manage product sales, and maintain our tools & equipment used for providing services in Asia."
.png)
“Our goal is to reduce the unplanned maintenance downtime to zero by keeping our workshop, machinery, tools, and equipment in good working order."

“We use ANEO Zero CMMS to enhance our overall control in our maintenance program, reflecting a much better follow-up in our preventive maintenance program, improve machinery repair cost evaluation to ultimately provide ready to use tools and equipment at any given time."

SERVICES
cloud-based
maintenance management system
WATCH VIDEO (15 MIN)
At ANEO Software company limited we know that businesses struggle with aging assets running to failure, so we developed ANEO Zero CMMS a computerized maintenance management system that is easy to use and helps you keep assets in good working order.
NEXT STEPS
I
CONTACT US
II
DEMO
III
PROPOSAL
RESULT
You Will Continue ...
-
Answering urgent service request and calls from your operations and customers;
-
Sending employees to inspect broken machinery and equipment to find out what needs to be repaired;
-
Searching for spare parts and materials and ordering missing ones with express delivery;
-
Explaining to your management, why operations are down due to maintenance.
You Will Focus on ...
-
Developing preventive maintenance programs for your new assets.
-
Planning work orders, allocating resources, and ordering spare parts and materials for upcoming projects.
-
Reporting completed maintenance, repair and overhauls;
-
Developing annual budgets in collaboration with your operations.
OUTCOME
PREVENTIVE MAINTENANCE
12 - 18 %
Studies indicate that implementing a proper predetermined preventive maintenance program can save as much as 12 - 18 % on the average compared to purely reactive programs.
PREDICTIVE MAINTENANCE
8 - 12 %
Implementing a properly functioning condition-based predictive maintenance programs can provide additional cost savings of 8 - 12 % over a program utilizing preventive maintenance alone.
FULL TRANSFORMATION
30 - 40 %
Depending on a facility’s reliance on reactive maintenance and material condition a full transformation from reactive to predictive maintenance could exceed 30 - 40 % cost savings.
IMPACT
OPEX
Lower Operating Expenses due to the reduction of maintenance downtime by 35 - 45 % and costs by 25 - 35 %.
CAPEX
Optimal Capital Expenditures due to the elimination of major breakdowns by 70 - 75 % and the minimized inventory.
ROA
Higher Return on Assets due to reduced maintenance downtime by 35 - 45 % and increase in production by 20 - 25 %.